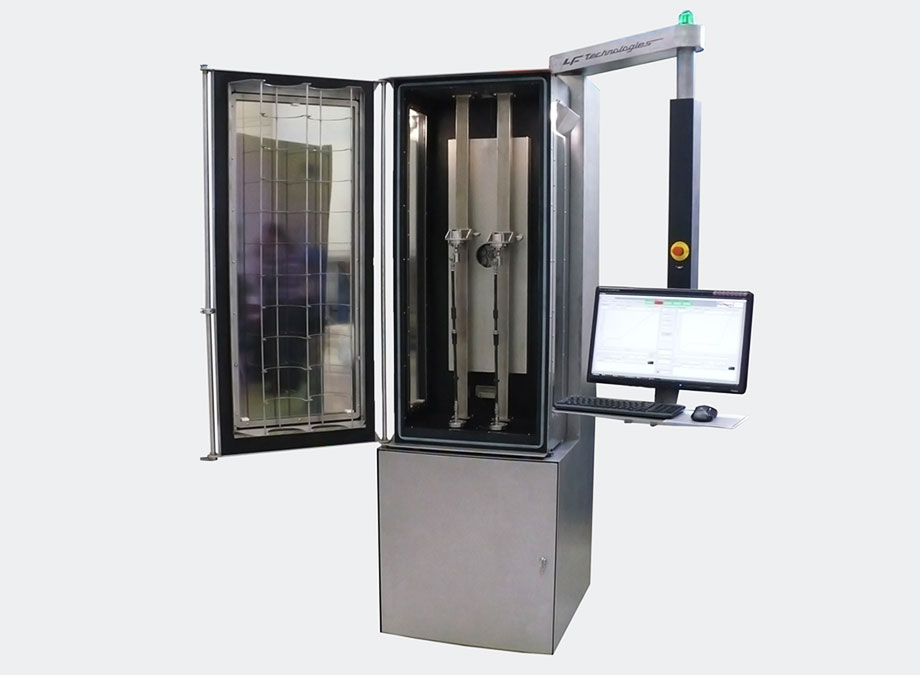
Pressure, burst, temperature bench
Design of a brake hose burst test bench. Hydraulic test of resistance to pressure, bursting and temperature. Carried out on 2 hoses at a time and in several stages.
THE SOLUTION PROVIDED BY LF TECHNOLOGIES
Main functions
Objective
Test high-temperature brake hoses in ramps and pressure steps until they burst.
The tests should be carried out in 4 stages: bleeding the hose, heating up and stabilising, building up pressure and maintaining it for several minutes, and increasing the pressure until it bursts.
Problematic Issues
The customer’s specifications included requirements such as a small footprint, the ability to test two hoses at a time and in a vertical configuration, etc.
Technical, operating, pressurisation and safety constraints were also imposed on us. It is essential that the test rig can be adapted to different hose lengths.
Solution and Result
Our expert teams have designed a bursting test bench capable of testing two hoses at the same time. The tests are carried out between 0 and 1800 bar in pressure and up to 200°C in temperature.
The hoses are housed in a thermal enclosure with a glass cover, which allows a high level of visibility of the products while ensuring the safety of the operators in the event of a rupture. The glass is resistant and has a self-cleaning treatment to facilitate maintenance and increase the life of the machine. To ensure that the bursting of one hose does not affect the other, the test rig has a wall to separate the two products.
The chamber is equipped with a temperature control system over the entire height of the chamber. At the bottom of the chamber is a sink to collect the ejected fluid, which is stored in a tank, with the possibility of being re-injected into the supply tank if it is deemed recyclable.
The test bench is equipped with a light source to make any faults visible and has a system to quantify any leaks.
The pressure build-up is perfectly controlled by servo cylinders associated with a pressure sensor.
To ensure the safety of the operators, the door of the pressure bursting test bench is closed by an electromagnetic safety lock. It prevents the temperature and pressure from rising if it is not locked and only opens if the safety conditions are reached (low temperature, low pressure). Before the test chamber is opened, a turbine forces the air to be renewed.
A light signal will also be visible during the entire test to avoid any danger.
The pressure burst test rig is capable of testing two hoses independently. A valve and a vertical slide adapt the test to the length of the hose.
The pressure test begins with the hose being bled of air before the test fluid is passed through.
The test rig then builds up the pressure to a specified level or according to a pre-programmed ramp. Once the plateau is reached, the pressure and temperature are maintained. This is done automatically, but the pressure build-up can also be controlled manually.
The operator selects the test parameters before starting the machine. He can choose :
- Bearing pressure
- Dwell time
- The rate of rise to bearing and burst pressure
- Temperature of the chamber.
At the end of the test, the burst pressure value is displayed on the pressure bench monitor.
Products tested
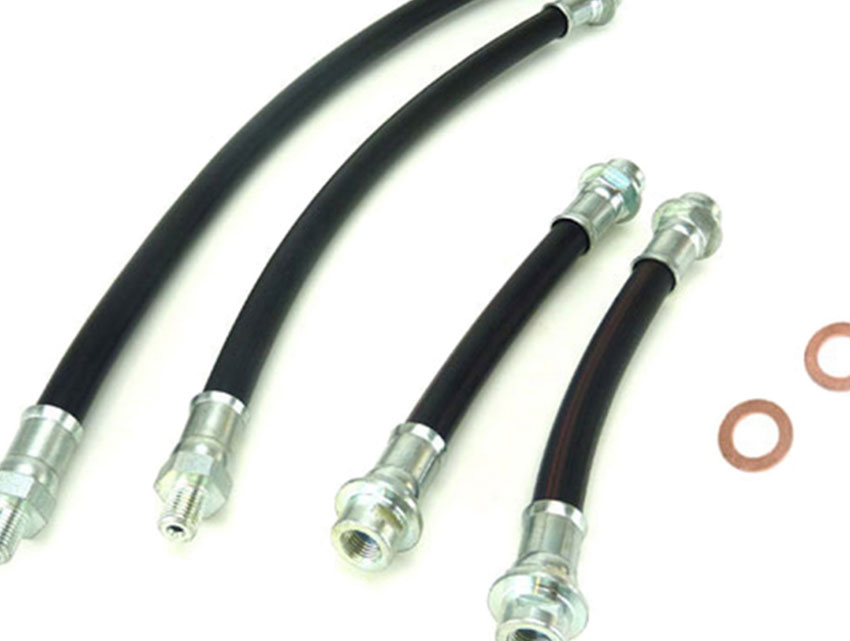
High-pressure brake hose
The brake hose is an automotive part, connected between a rigid hose and a brake caliper, which allows the flow of brake fluid (DOT oil).
OUR KEY TEST BENCH FOR THESE TESTS High Pressure, Burst and Temperature Test Bench for Hoses and Pipes Perf-HP
The software can automatically generate pressure and temperature ramps and detect hose bursts.
A low-pressure booster pump draws liquid from a reservoir. This liquid is discharged via a valve into a small vertical chamber.
The upper part of the chamber is located inside the thermal enclosure. This chamber is fitted with a removable part that houses the fittings for adapting the lower part of the hose under test.
The upper part of the hose under test is connected to a pilot valve, mounted on a vertical slide, allowing the hose under test to be adapted to its length.
A pressure sensor on the body of the vertical chamber measures and transmits the pressure applied to the hose.
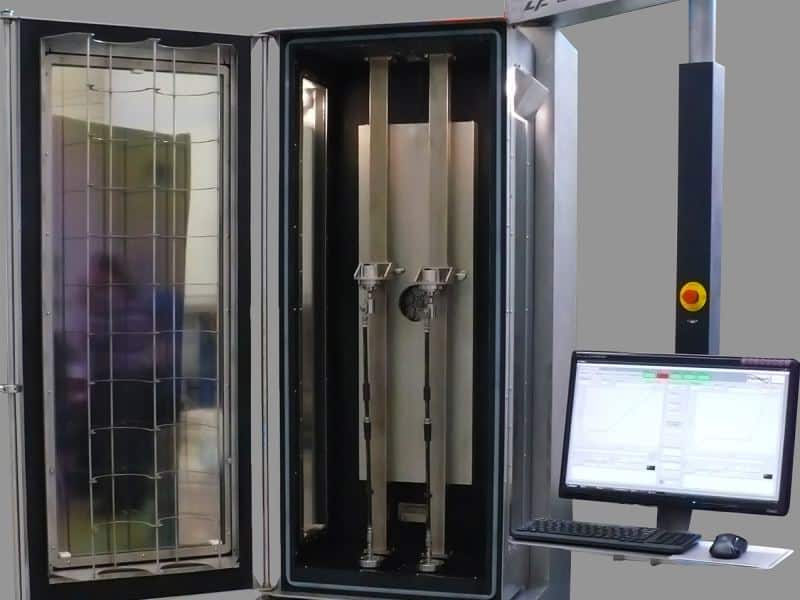
Bench developed to meet these standards:
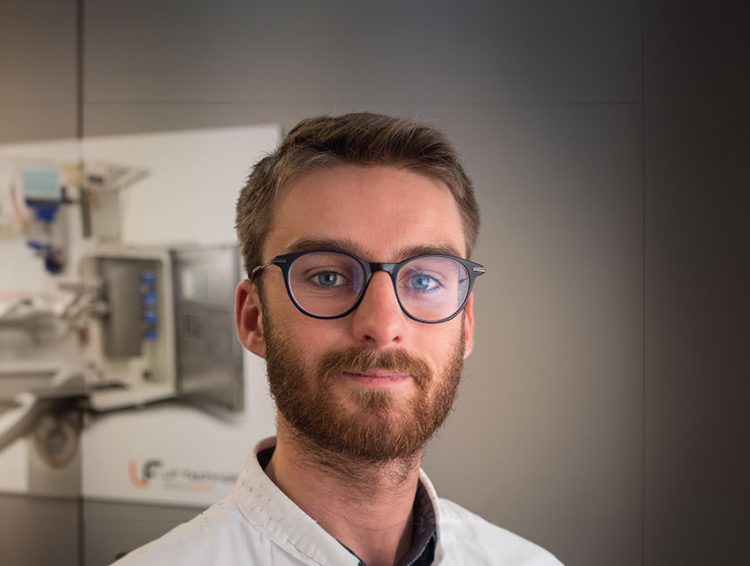
Do you have a project in mind ?
I'm here to advise you and propose solutions tailored to your needs.
Aurélien Cottin
Hydraulics Division
Other sector applications
Discover other test benches and special machines designed by LF Technologies.