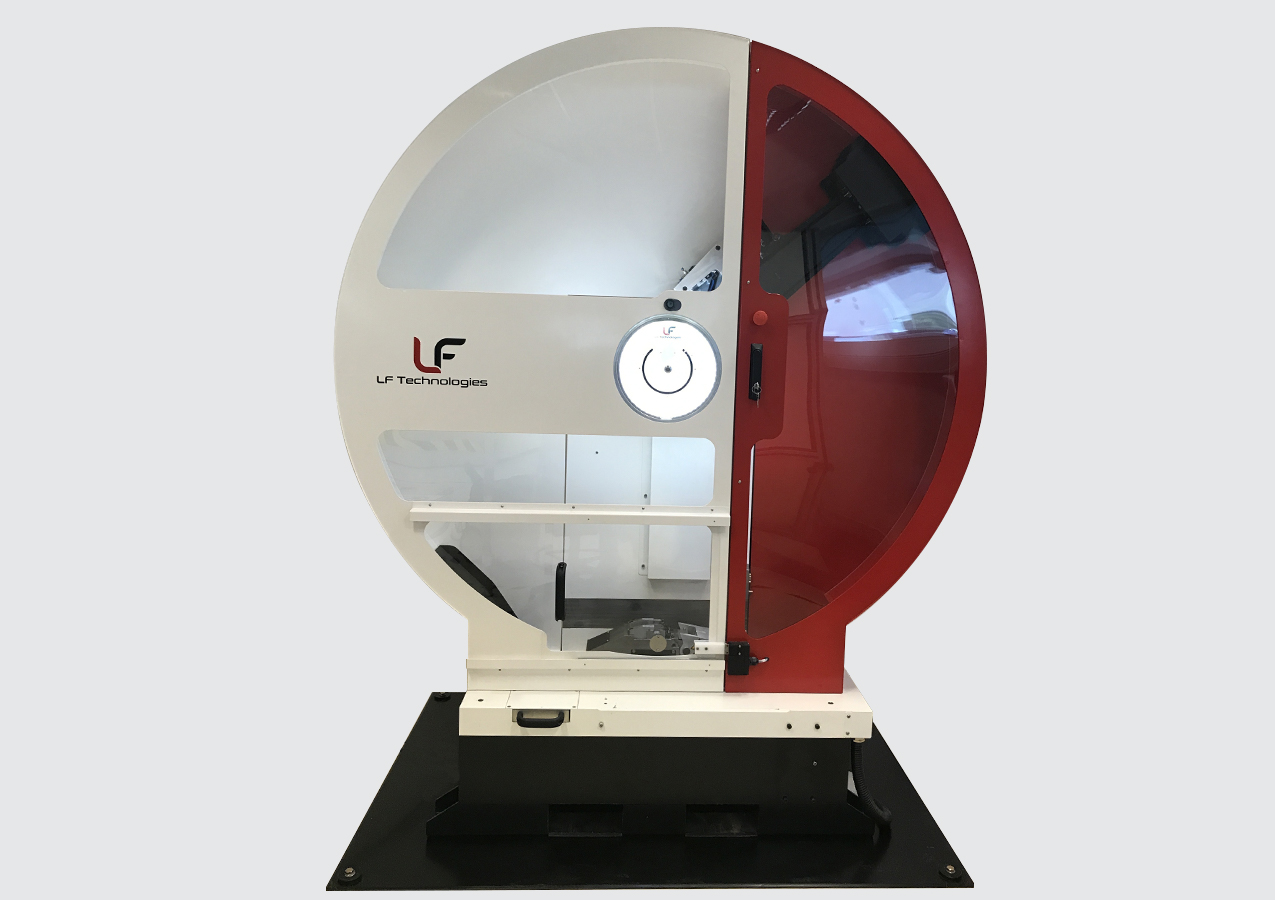
Impact pendulum Research and Development
Pendulum impact bending tests on Charpy specimens in accordance with standards NF EN ISO 148-1, NF EN ISO 148-2, NF EN ISO 148-3 and NF EN ISO 14556.
THE SOLUTION PROVIDED BY LF TECHNOLOGIES
Our client is a research and development centre specialising in materials.
Main functions
Objective
Carry out impact bending tests on Charpy specimens in accordance with standards NF EN ISO 148-1, NF EN ISO 148-2, NF EN ISO 148-3 and NF EN ISO 14556, with an automatic specimen temperature control system, from -180°C to +600°C.
PROBLEMATIC ISSUES
The problem of the impact pendulum
- To ensure automatic positioning of the pendulum as well as on-the-fly catch-up after impact.
- Ensure that the arm catches up after the impact so that the specimen is not re-taped after the first impact (making the test null and void as it is impossible to study specimen falls).
- Reliable force/displacement measurement that is easy to calibrate
- Facilitate verification and calibration procedures for the imapct pendulum
Thermal enclosure issues
Impact bending tests are performed in accordance with standards. In the case of temperature tests, these standards require specimens to be brought to temperature and conditioned strictly: temperature control, measurement location, distance between specimens, and transfer time between the thermal chamber and the pendulum. Once heated, the specimen must be placed on the pendulum and tested within 5 seconds of leaving the chamber.
SOLUTION AND RESULT
Imapct pendulum
The specimen support is fitted with a centering device. This device presses the specimen against the supports and ensures centering just before impact. The specimen is centered by its notch. The pendulum arm is linked to a motorized arm. This motorized arm follows (without touching) the pendulum arm during release, and reattaches it on the fly. This motorized arm also enables the pendulum arm to be raised to the desired release height. The machine is equipped with a number of control systems to check pendulum geometry, moment and load cell response, enabling direct verification in compliance with the standard.
Thermal enclosure
LF Technologies has imagined and designed a thermal enclosure with a test-tube conveyor. This conveyor ensures compliance with the spacing between test specimens required by standards. The thermal chamber is also equipped with a system for transferring test specimens to the pendulum. This transfer system consists of a “scoop” which positions the specimen in the pendulum. The movements of the “shovel” and the pendulum are synchronized, ensuring very short transfer times (time between temperature conditioning exit and shock less than 5 seconds). The thermal enclosure enables temperature control from -180 to +600°C, while ensuring efficient specimen temperature setting and transfer.
Tested product
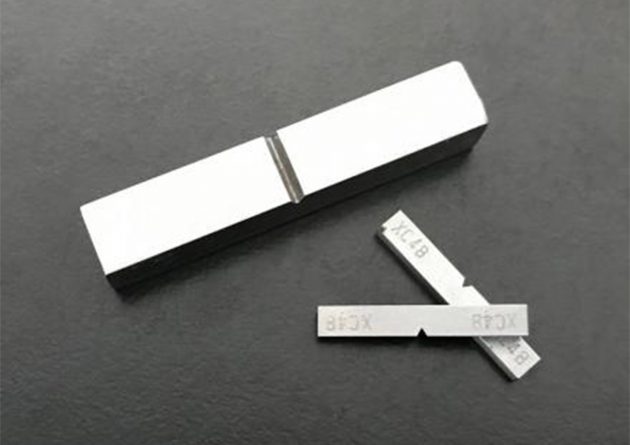
Steel test tubes
The steel specimen is a characteristic sample of the material to be tested. The aim of the impact bending test is to determine the energy required to break the specimen, thus characterizing the material’s resilience. The type of impact (force/displacement curve) can also be used to determine certain specific characteristics of the material. The impact bending test can be carried out at room temperature, or with a temperature-conditioned specimen. For a given material, the variation in impact strength as a function of temperature can be used to determine a curve corresponding to the evolution of the material’s strength as a function of its temperature.
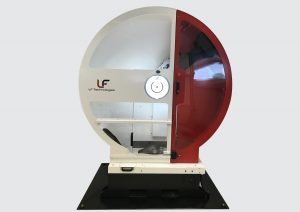
Impact pendulum Research and Development
Impact pendulum Research and Development
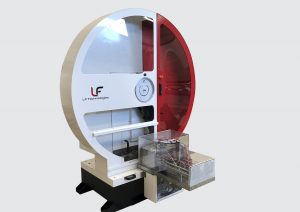
Pendulum hammer + thermal enclosure
Pendulum hammer + thermal enclosure
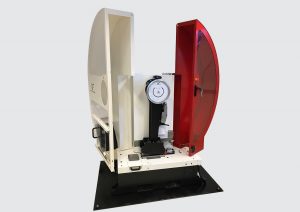
Impact pendulum test bench open house
Impact pendulum test bench open house
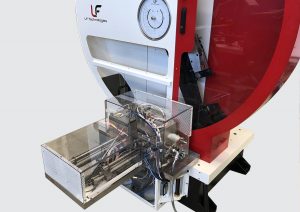
Impact pendulum test bench and thermal enclosure
Impact pendulum test bench and thermal enclosure
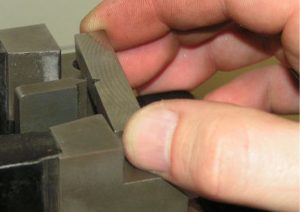
Installing the test piece in the test area
Installing the test piece in the test area
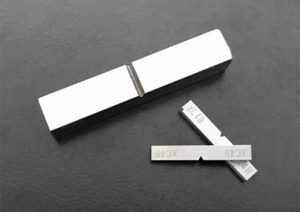
Impact pendulum test bench test tube
Impact pendulum test bench test tube
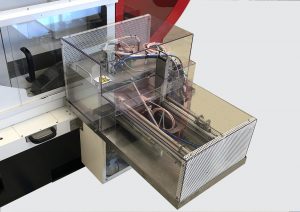
Thermal enclosure
Thermal enclosure
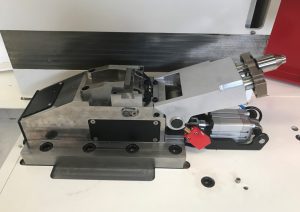
Mobile Impact pendulum test bench carriage
Mobile Impact pendulum test bench carriage
Impact pendulum Research and Development
The test rig is a pendulum impactor with a U-shaped hammer that can be fitted with different weights to perform tests ranging from 300J to 800J.
OUR KEY TEST BENCH FOR THESE TESTS Impact pendulum – Impact Charpy, Izod MCMP
Main functions
Impact resistance is one of the most important properties to study when designing a part or appliance. The LF Technologies sheep-pendulum impact tester is used to determine the resilience of a specimen to an impact generated on it, in accordance with ASTM and ISO standards. Our impact and pendulum impact testing machines perform precise, repeatable impacts on a wide range of materials to determine the mechanical and physical characteristics of metals, polymers, composites and finished products, whether for R&D or quality control. Our machines perform Charpy and Izod tests, which meet international standards.
Operating mode
The automatic specimen centering system ensures simple, efficient use of the pendulum impactor. Specimens are impacted within 5 seconds of removal from the temperature unit. Operation is simplified by quick-change knife and specimen supports. The motorized pendulum hammer is equipped with a pneumatic hammer release system. Hammer reset is motorized for ease of use. A protective guard protects operators while the hammer is in motion.
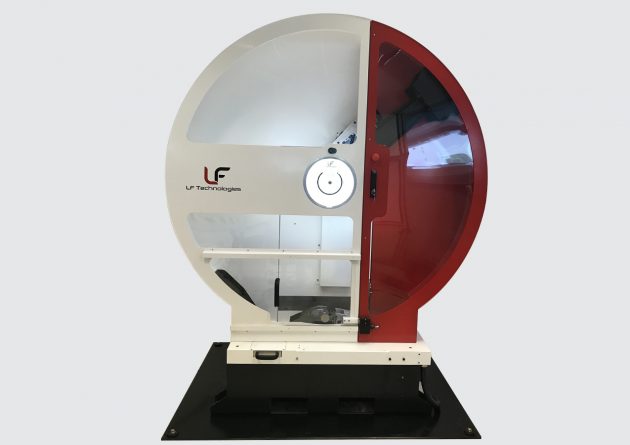
Bench developed to meet these standards:
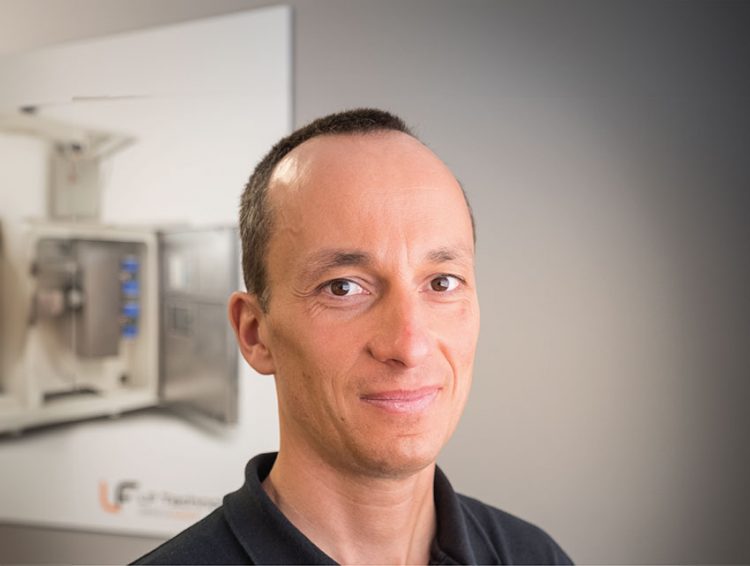
Do you have a project in mind ?
I'm here to advise you and propose solutions tailored to your needs.
Benoit Pelloquin
Mechanical Division
Other sector applications
Discover other test benches and special machines designed and built by LF Technologies.