Our customer is a medical device manufacturer, specializing among other things in the manufacture of respiratory assistance devices used in hospitals, essential in the treatment of respiratory diseases such as Covid-19.
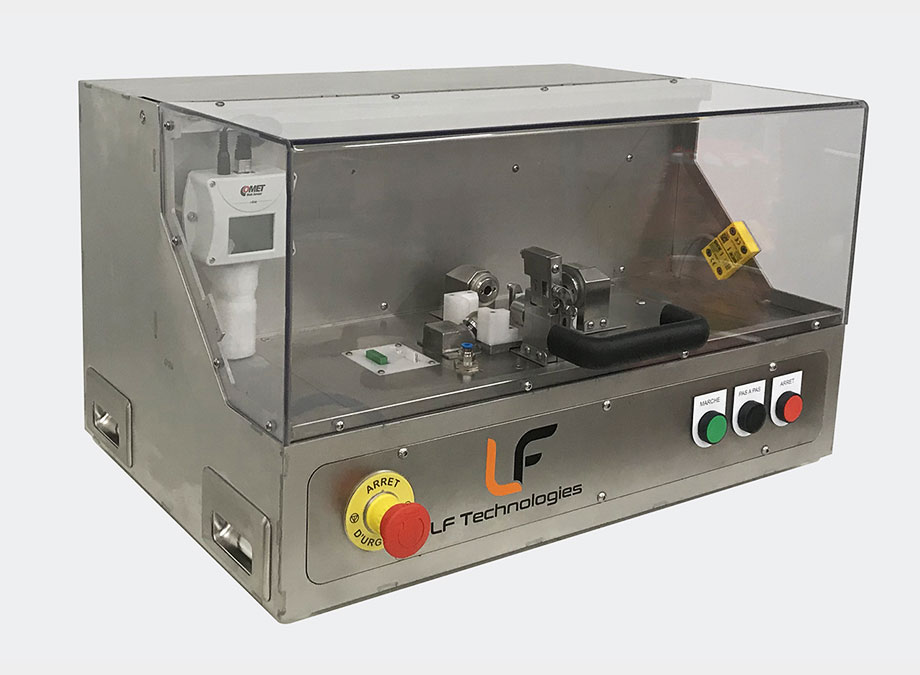
Test bench for medical ventilation equipment
Test bench for respiratory assistance devices used in hospitals.
THE SOLUTION PROVIDED BYLF TECHNOLOGIES
Main functions
Objective
These artificial respirators are made up of several components that control the flow, pressure and rate of oxygen delivered to the patient.
Our customer’s objective is to integrate, upstream of the assembly of flow control sub-assemblies on the final product, validation checks on these sub-assemblies. The aim is to detect any non-conformities as early as possible in the manufacturing process, without waiting for the final product to be inspected.
Issues
Our first problem consists in building 2 independent test benches, to test 2 relatively different components, but our customer wants these two benches to be built on an identical base, with different equipment options, and identical control software.
We also have severe space constraints, which means we have to design a small test area.
The testing of these products, their clamping and their connection to the bench must be automated.
The test must be carried out with a high level of traceability, for all measurement and control points.
Solution and Result
The equipment proposed is a set of two test benches equipped with more or less options, and with test plates specific to each product.
To overcome space constraints, each bench is designed in two separate parts:
- 1 small test area on a workbench
- 1 remote electrical and pneumatic control system near the bench (identical for both machines).
Medical device components undergo air-tightness tests, flow measurement and verification of all their functions.
The software, developed in-house, enables test programs to be edited, measurements and graphs to be visualized, and results to be saved. These results are stored in an SQL database that integrates seamlessly with our customer’s product data management system.
Safety is ensured by a range of systems, including a polycarbonate hood to protect against splashing, and an emergency stop to cut off the air supply and stop the test in progress.
Products tested
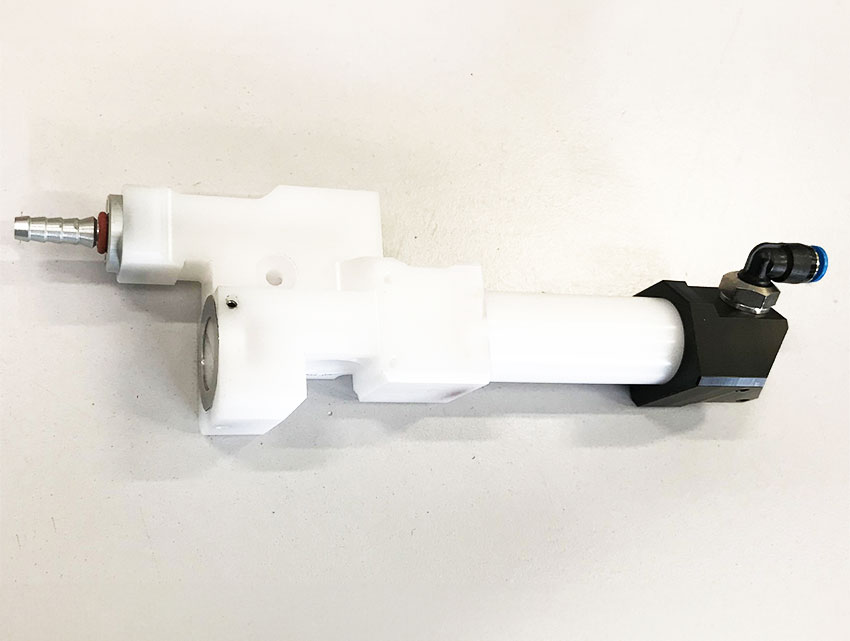
Respiratory assistance devices
Breathing aids comply with stringent safety standards, and are subject to numerous checks on the production line. The qualification of each respirator is validated by a thorough final inspection.
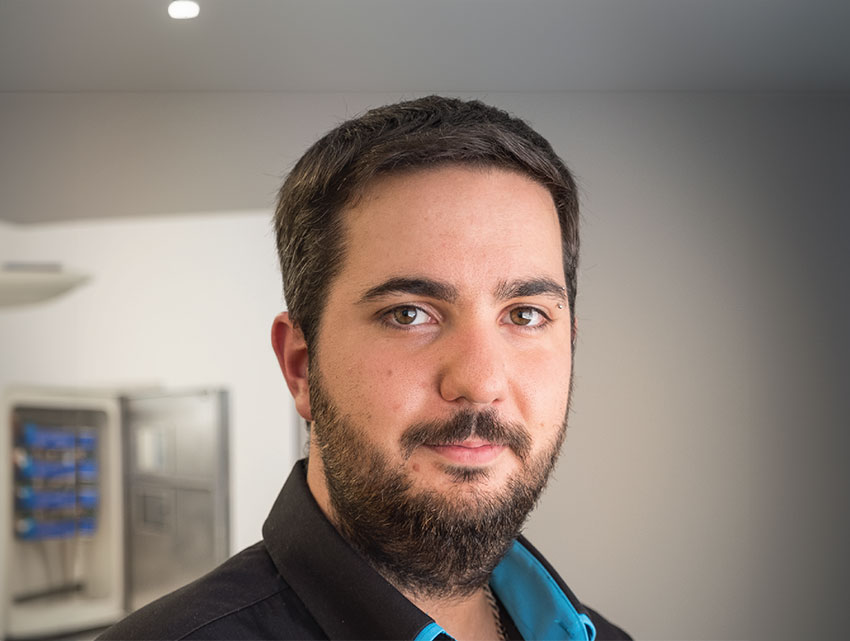
Do you have a project ?
I will be happy to advise you and propose solutions tailored to your needs.
Kevin Imberte
Special Machines Division
Other sector applications
Discover other test benches and special machines designed by LF Technologies.