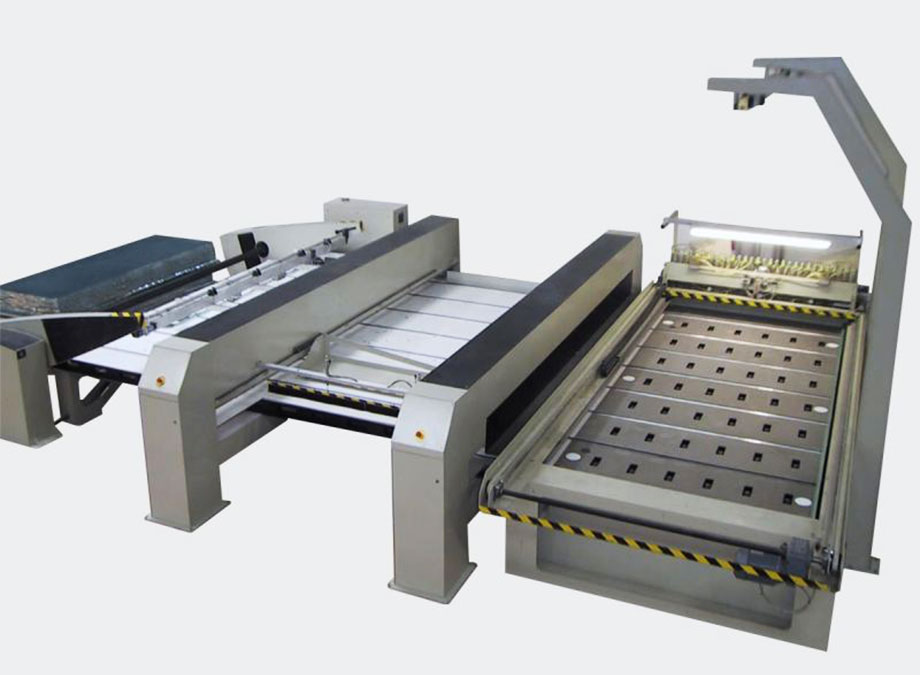
Honeycomb expansion machine
- Strong productivity gains
- Perfect repeatability
- A very short set-up time
- Better material yield
Products tested
Sector of activity
Product Manufactured
Honeycombs are structures used to reinforce the strength of an element, while guaranteeing great lightness; Often placed in the centre of a sandwich structure, honeycombs can be made of aluminium, composite, cardboard or plastic;
Functionality
Automated stretching of aluminium honeycomb panels using an expansion machine;
The honeycomb expander must offer perfect repeatability, very short set-up times and a high level of automation;
Design and Manufacture
LF Technologies designed and developed an expansion machine according to the customer’s specifications in order to perfectly meet the required application;
The expansion machine consists of 2 crosspieces, one fixed and one mobile, positioned so that the bottom stops form an introduction channel for the honeycomb “slice” to be stretched; This is inserted laterally by means of a slide and held under slight pressure by the mobile crossbar;
30 needles are lowered by some thirty jacks (15 per sleeper), initiating the pointing corresponding to the penetration zone, before crossing and fitting into the lower guide bushes, thereby authorising the traction cycle; The machine has a total draw stroke of 4,500 mm; Maximum traction force; can reach 10,000N;
The needle spacing is motorised and servo-controlled; During stretching, the needles automatically move closer together to support the product’s natural width shrinkage;
The expansion machine is equipped with an electric control console to operate the whole unit; A PC manages all the machine’s functions and an interface screen is used to display and set the various parameters;
Safety is ensured by 4 emergency stops, a bonnet system to protect the area where the needles are lowered, and regulatory safety features such as light barriers to enable pallets to be removed from finished products in complete safety;
The equipment offers the following advantages:
Benefits
- Strong productivity gains
- Perfect repeatability
- A very short set-up time
- Better material yield
- A regular expansion
Honeycomb expansion machine
Automated stretching of an aluminium honeycomb panel using an expansion machine;
ADD-ON MODULES
Explore our add-on modules to get the most out of your special machine !
Discover innovative solutions to further enrich your experience and optimize your results.