Project Progress
Our team of experts works on the design of your machine from the pre-study phase to commissioning.
Solidworks drawings, electronic boards, software, assembly, on-site installation, technical documentation, etc. are all tailor-made by our engineers. Everything is tailored to your project. Everything is tailored to your project.
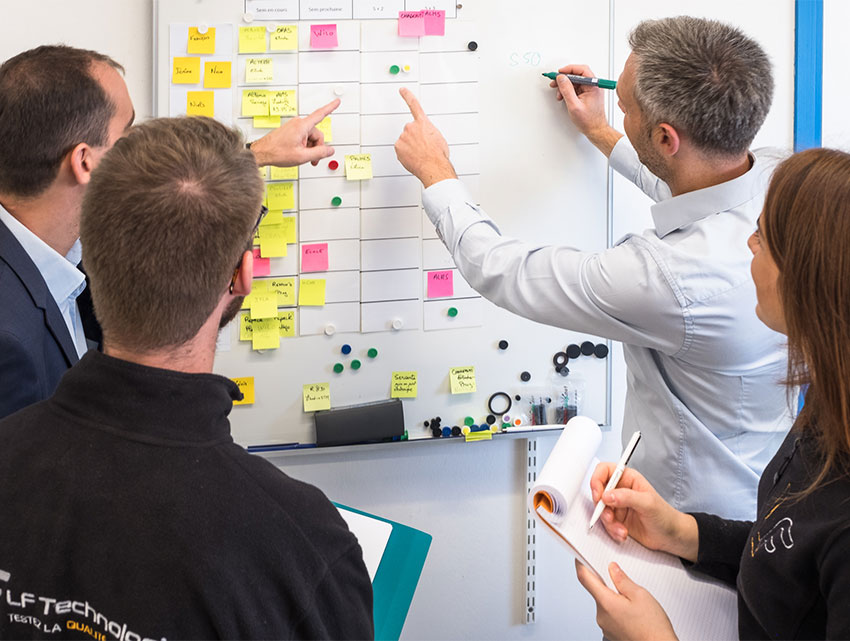
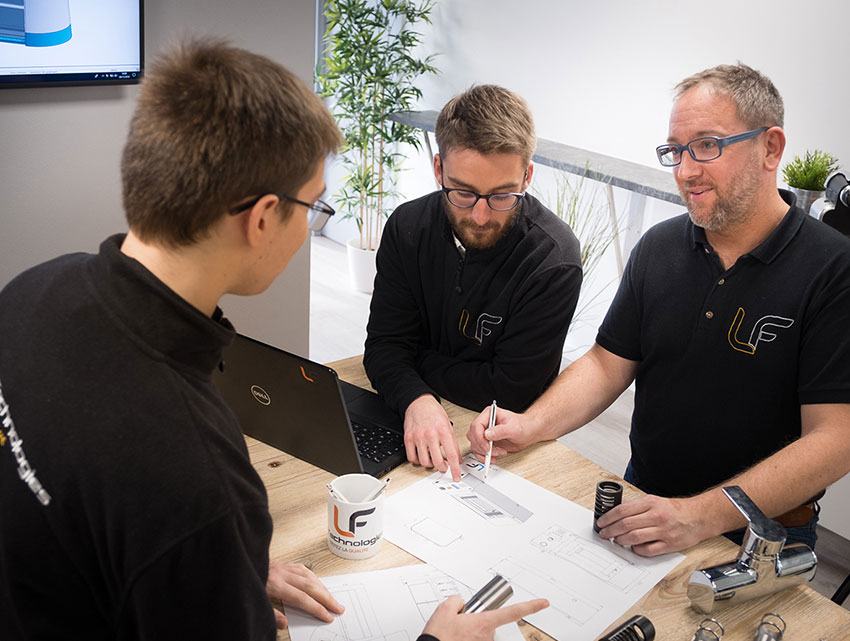
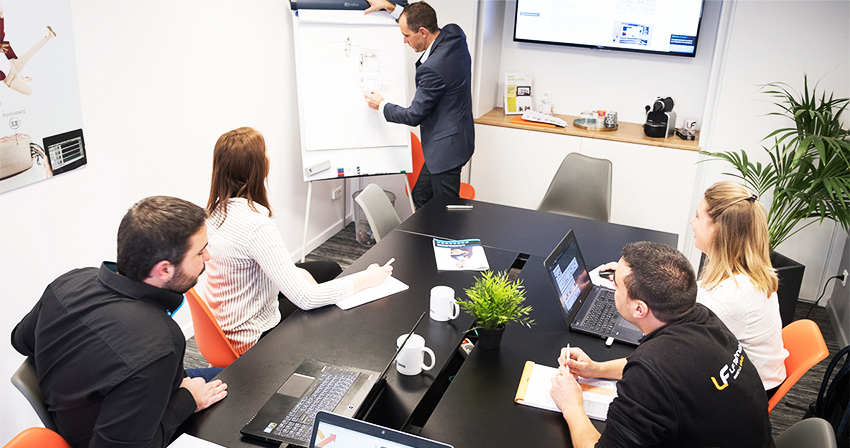
1 – PROJECT MANAGEMENT
Our team of engineers and technicians will support you throughout your project, from the technical proposal to the design and assembly stages, right through to the commissioning of your machine.
After delivery and/or commissioning, our after-sales service is available. We are also able to offer you various services via our maintenance contracts.
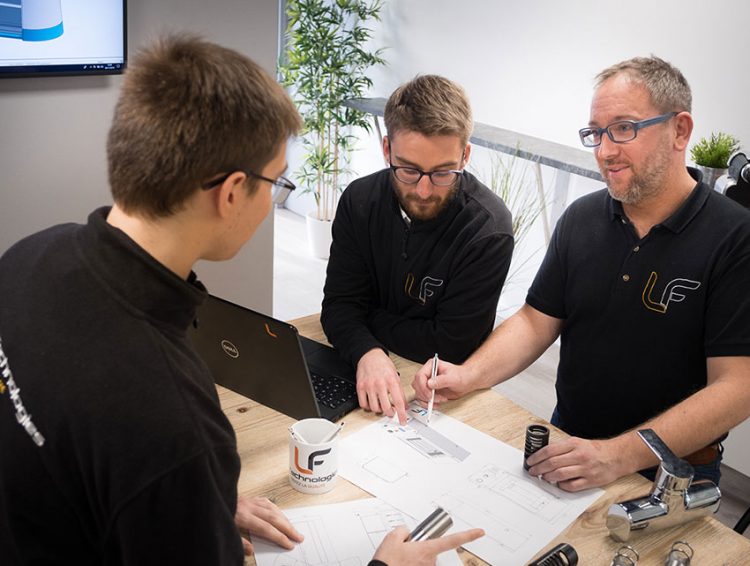
2 – TECHNICAL PROPOSITION
Our sales department studies your specifications and evaluates the feasibility of your project, taking into account all its specificities.
Our pre-design team can then draw a first CAD draft of your machine according to your different requirements and technical constraints.
We provide you with a turnkey technical and financial offer as a basis for negotiations between our commercial and technical teams.
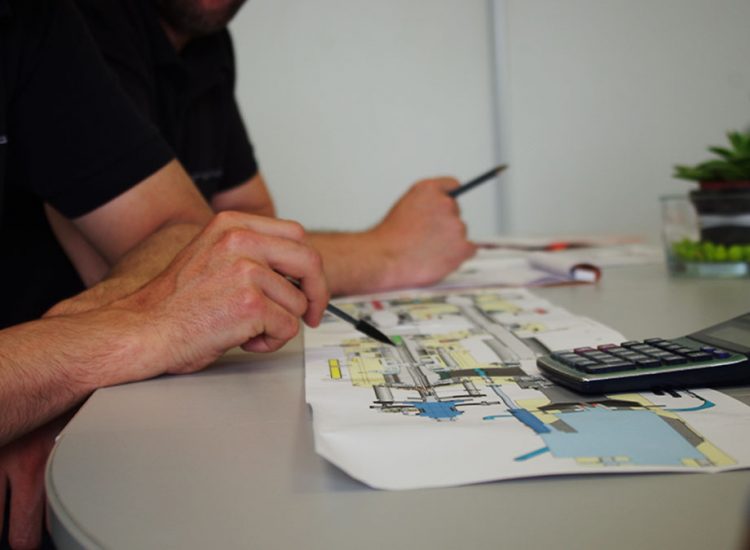
3 – PROTOTYPING
Our technical teams can produce a non-definitive prototype (test assembly) in order to demonstrate the feasibility of your project, allow its technical validation, and define the optimal solution according to your constraints.
At the end of this test phase, data analyses are carried out and a technical test report is issued. These allow our technical teams to finalise the solution and to propose the best technical and commercial turnkey offer.
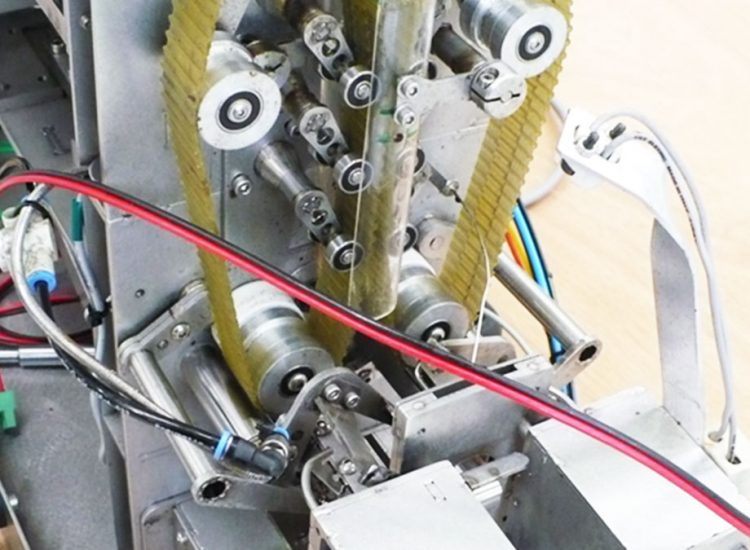
4 – LAUNCH
A project manager is assigned to your file and becomes your contact person throughout the project.
An initial kickoff meeting is scheduled between the LFT staff and your technical contacts to introduce each team member, clarify roles and establish a partnership.
A schedule of the progress of the case is drawn up.
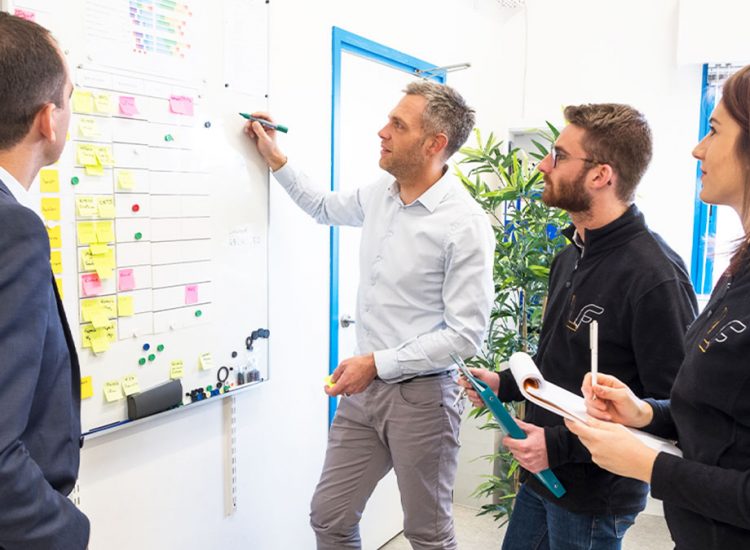
5 – STUDY
Our engineers and technicians study and design your machine through several stages:
Pre-study :
- Pre-selection of components
- V1 synoptic (general graphic presentation) of the project
- Start of the drawings
- Calculation notes
Study :
- Programming synoptic
- Complete bill of materials (mechanical, electrical, etc.)
- Finalisation of diagrams and synoptics
- CAD files, mechanical simulation
- Calculation notes
- Risk analysis
- Visit to certifying body (Apave, etc.)
- HMI test
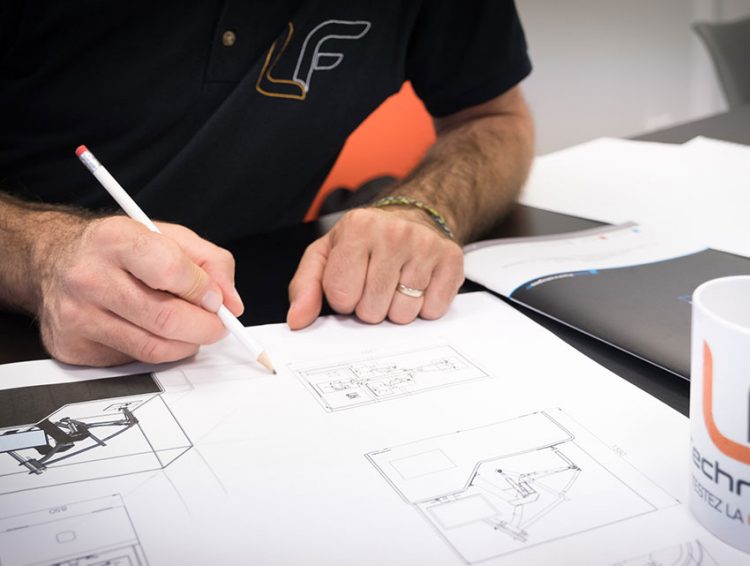
6 – MANUFACTURING
Once the study has been validated by your technical department, the production drawings are drawn up and the component parts lists are sent to the purchasing department to place orders with suppliers.
The parts received undergo verification and quality control as they are received at our site and are then distributed according to the different projects.
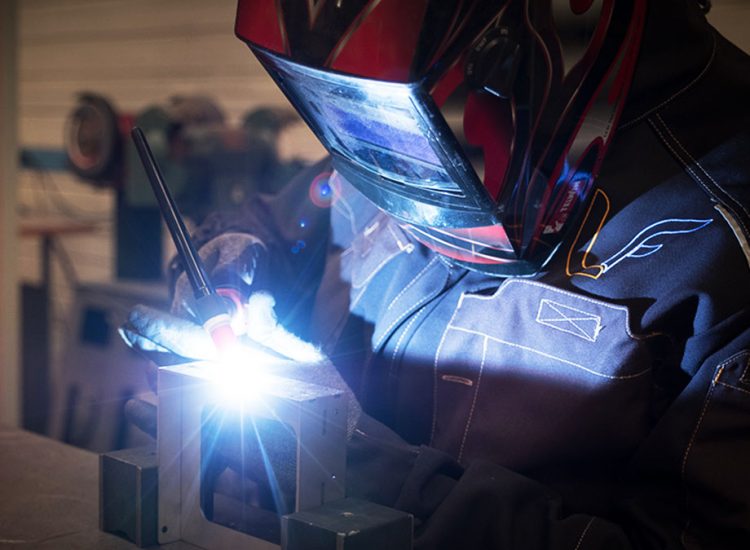
7 – ASSEMBLY AND INSPECTION
Mechanical, electrical, pneumatic and hydraulic assembly, soldering of electronic cards and installation are carried out by our fitters in our workshops.
In parallel, our LabVIEW developer designs a program according to your specifications and according to a charter defined by LF technologies (ergonomics, intuitiveness, ease of use, etc).
The tuning and testing phase takes place once the test machine is fully assembled and wired.
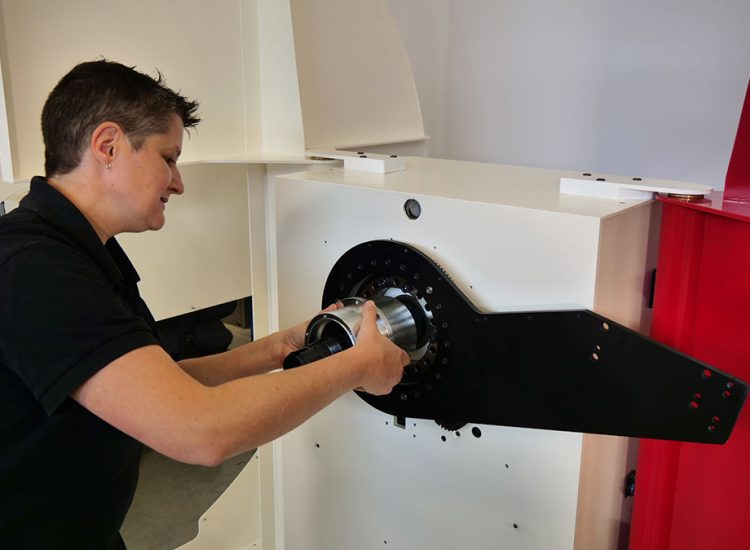
8 – COMMISSIONING
We schedule a technical test on our premises with your technicians.
Technical acceptance: stage where the customer validates the solutions chosen, even when they differ from those provided for in the order or at the end of the study. At this stage, all the functions of the machine can be validated independently of the complete automation system.
Once the final corrections have been made, a complete and final checklist is carried out by the project manager to ensure that everything is in accordance with the CDC, the order, any amendments, etc.
Our logistics team organises the transport and plans the commissioning on your site.
During commissioning, we provide training for the bench users.
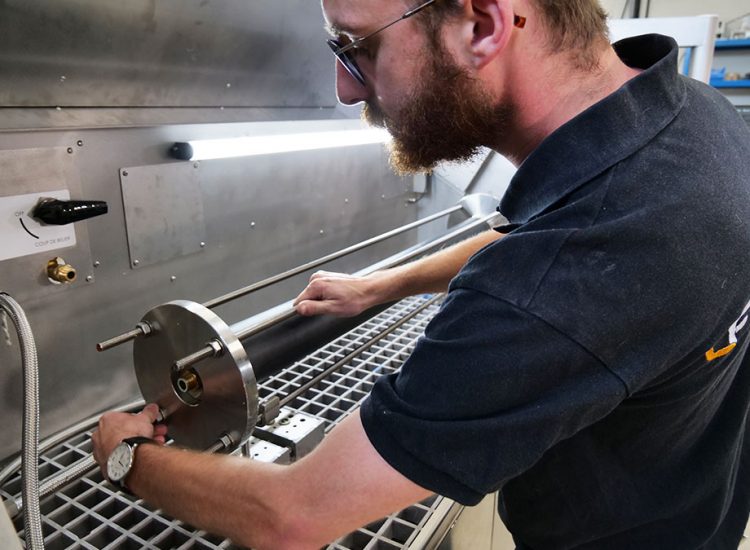
Our support solutions
In addition to our warranty, we offer support for your machines through our maintenance solutions. We can intervene on spare parts changes, sensor calibration or answer your questions related to the use of your test bench or production machine.
We offer maintenance contracts (LF’Assist) adapted to your needs, including audit and preventive interventions, telephone assistance hours and controlled time breakdown interventions.
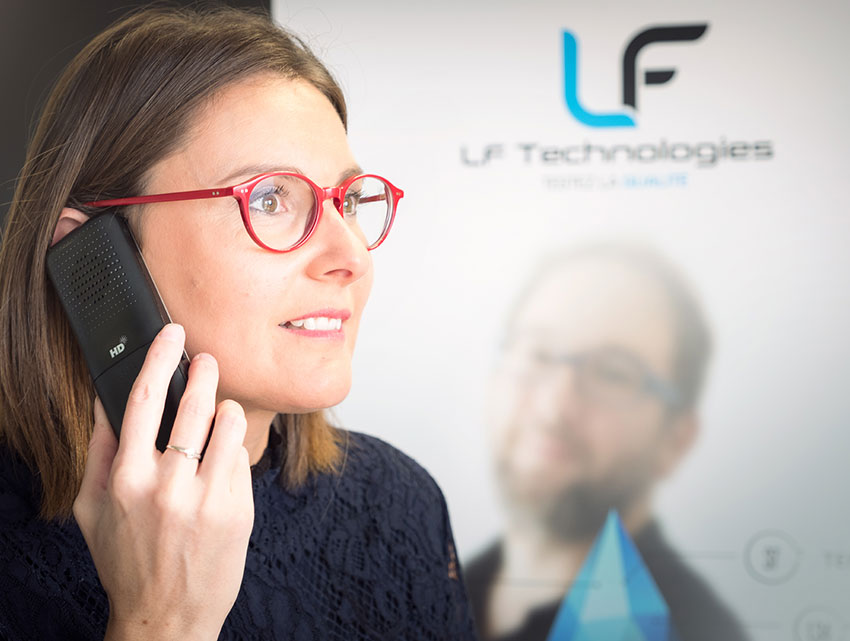
Project management in the design of special production machines
The success of a special-purpose machine design project in the industrial sector is of vital importance to the competitiveness of LF Technologies. Project management plays an essential role in coordinating the various stages of development, guaranteeing the creation of high-performance equipment that meets customers’ needs.
Rigorous front-line planning
The crucial initial step in the successful design of special production machines is rigorous planning. This phase defines the objectives, resources required and deadlines to be met. It also requires anticipation of potential risks, accompanied by preventive solutions.
Planning tools
To facilitate planning, we recommend the use of tools such as:
- Project management software to organize tasks, allocate resources and track project progress.
- An online graphic visualization, providing an overview of the project and highlighting the links between the various tasks.
Communication: the key to success
Maintaining fluid and regular communication within the team is essential to ensure the smooth running of the special machine design project. Sharing information, clarifying responsibilities and resolving problems quickly are imperative.
Communication tools
To encourage communication within the team, several solutions can be put in place, including :
- Setting up a collaborative platform to centralize project information and facilitate collaboration.
- Regular meetings and videoconference calls to review project progress and discuss any difficulties.
Expertise required
The realization of a special production machine design project requires the convergence of different areas of expertise, such as :
- The design office, responsible for drawing up equipment plans and diagrams in line with customer requirements.
- Research and development (R&D), which works on the continuous improvement of machines and the integration of new technologies.
- Manufacturing, made up of technicians and workers specialized in machine construction and the assembly of mechanical, electrical and hydraulic components.
- Automation and control, responsible for developing and programming automated systems to control machines;
- Maintenance and after-sales service, intervening in the event of malfunctions to ensure long-term optimal operation.
Technological innovation at the core of the project
Technological innovation is at the core of the design of special production machines. This includes :
- Integrating the latest advances in artificial intelligence (AI) and the Internet of Things (IoT) to improve machine efficiency and flexibility.
- The development of augmented reality solutions to facilitate operators’ work and optimize maintenance.
- Exploiting the possibilities offered by additive manufacturing technology (3D printing) to simplify the production of complex parts and reduce costs.
These innovations make LF Technologies’ machines more competitive, while meeting today’s environmental and social challenges.
Quality Culture and Continuous Improvement
To guarantee the success of a special-purpose machine design project, it is imperative to establish a culture of quality and continuous improvement. This implies :
- Unite LF Technologies teams around values such as operational excellence, commitment and customer satisfaction.
- Establish a quality management system (QMS) based on international standards (ISO 9001), involving all LF Technologies employees in a continuous improvement process.
- Set up key performance indicators (KPIs) to measure the efficiency of the design process and track project progress.
- Carry out audits and identify areas for improvement to correct weaknesses and promote best practices.
Thanks to rigorous planning, effective communication, adapted skills, a constant approach to innovation, and a culture of quality, LF Technologies can successfully meet the challenges of project management in the design of special production machines.