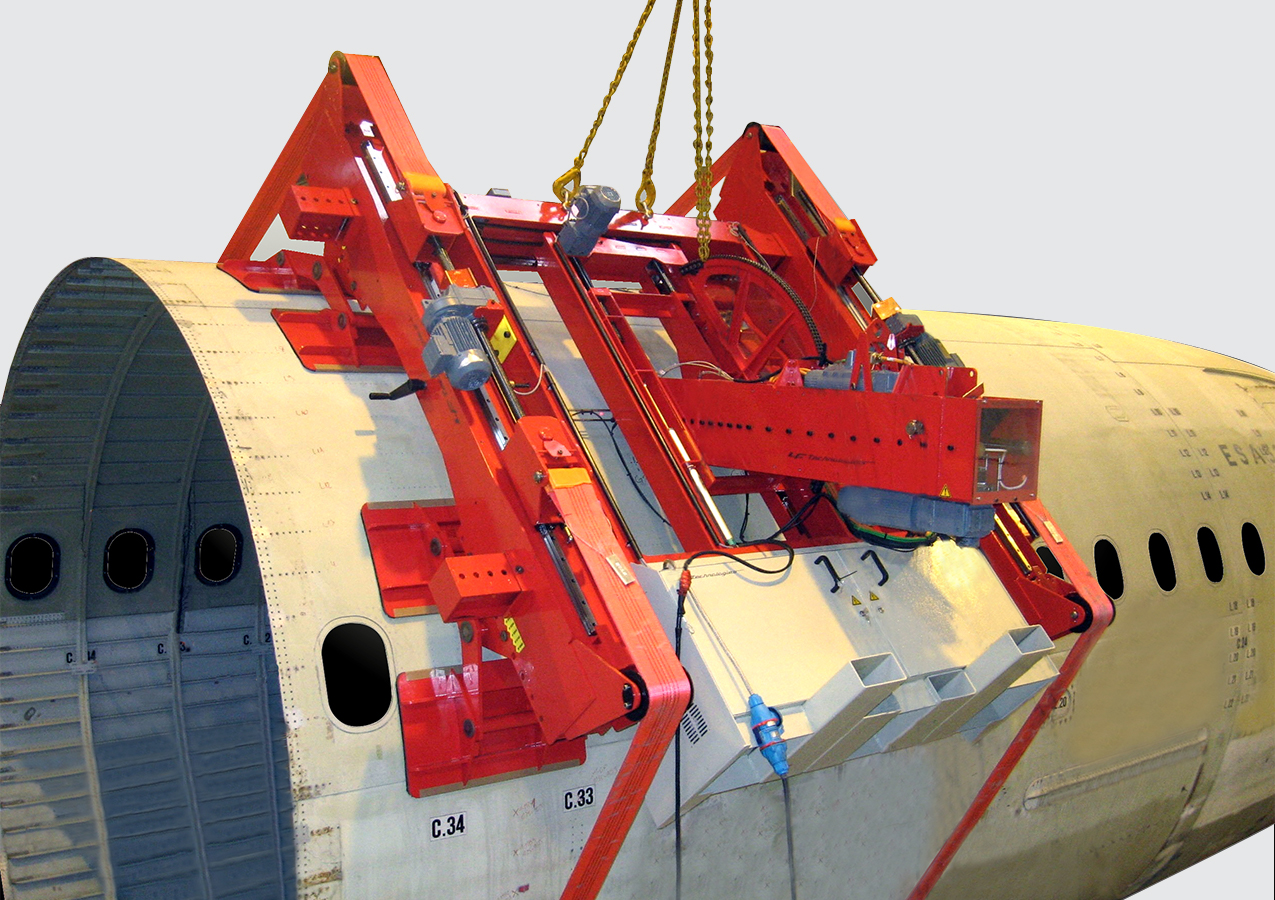
Impactor Static Dynamic combined
- Autonomous attachment to the product under test using self-tightening straps
- Shooting possible in all directions with motorized settings
- Precise shot positioning with automatic X/Z adjustment and laser sighting
- Position of support pads adjustable to suit diameter of product under test
Products tested
Sector of activity
Main functions
The combined static/dynamic impactor enables impact tests to be carried out in any orientation (horizontal or vertical). The shocks are generated by a linear ram driven by an electric servomotor. By measuring position and velocity relative to the impacted object, we can measure the potential energy of the impact and the energy absorbed by the sample. The position and orientation of the impact are adjustable and motorized. The bench can also perform static compression tests up to 80 kN.
Operating mode
The machine is attached to a test stand or directly to the component to be tested. This is achieved using a system of automatically controlled tightening straps, eliminating the need for a large gantry (for testing on an aircraft, for example). The user sets the position and orientation of the impactor. The test bed automatically searches for a contact position. The impactor is then propelled at a controlled speed over the product/sample. The impactor is automatically caught up to avoid rebound shocks. The differential impactor/target position is measured by laser.
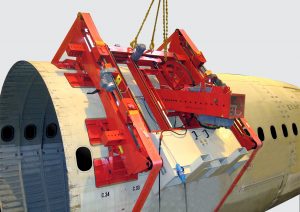
Combined static-dynamic impactor
The dynamic test bench enables impact tests to be carried out in any orientation (horizontal or vertical).
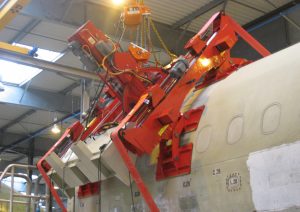
Hanging
Autonomous attachment to the product under test using self-tightening straps.
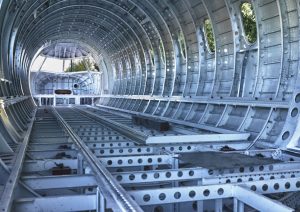
Airframes
Simulated impact between a runway vehicle and an aircraft on the tarmac.
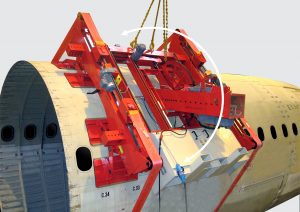
Orientation
Shooting possible in all directions with motorised adjustments.
Impactor Static Dynamic combined
Impact tests on the fuselage of a “test” aircraft. The tests carried out are used to reproduce deformations, in order to estimate the force, energy and impact velocity criteria that generate this type of defect.
Advantages of the Combined Dynamic Static Impactor
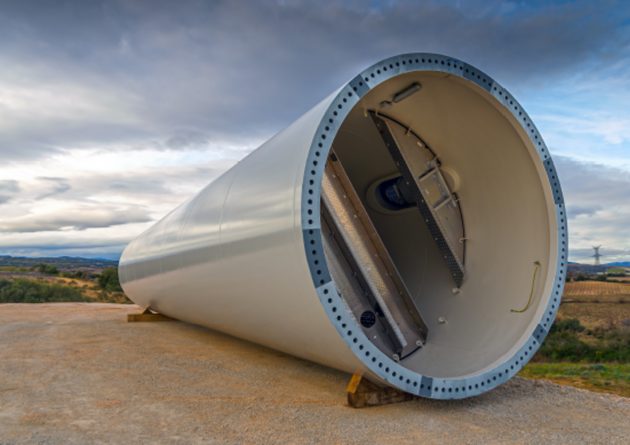
Wind turbine mats
Simulation of impacts on a wind turbine mast.
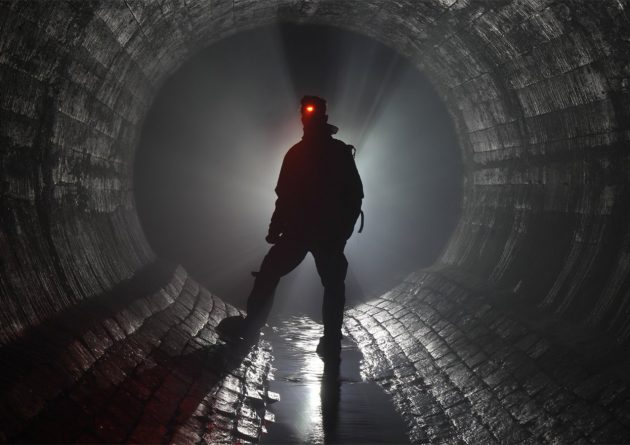
Large-diameter tubes
Behavior of a tube subjected to a static point load.
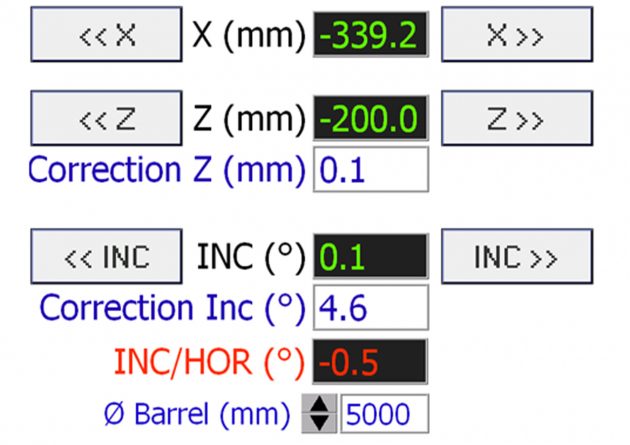
Positioning
Precise shot positioning thanks to automatic X/Z adjustment with laser sight.
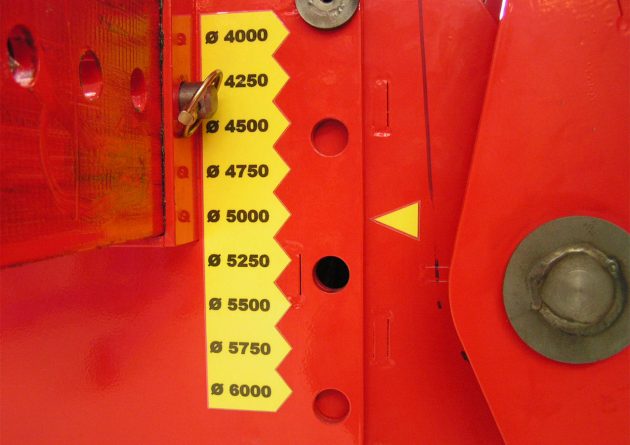
Diameter adjustment
Adjustable pad position to suit product diameter.
TECHNICAL SPECIFICATIONS of the Combined Dynamic Static Impactor
Specifications | MCI |
Machine | |
1 impactor body with carriage drive and guide 2 Ø 50 mm rails | |
1 trolley with 8 rollers for impact tests up to 500 J. (dynamic tests) | |
1 electric servo jack 80 kN (static tests) | max. stroke 300 mm |
2 beams whose spacing can be adjusted from 2 100 mm to 2 600 mm | |
- 8 foam rubber pads | 700 mm × 400 mm |
- 1 strapping system: max. strap pulling force | 30 kN/brin |
2 laser support ramps | |
- laser measurement to compensate for chassis deformation | |
- pointing laser | |
1 remote control controlling the strap tightening and impactor orientation motors | |
1 specific software package controlling the system and analysing the measurement results | |
Machine features | |
Energy impact | 50 to 500 J. |
Impact speed | 1.2 to 4 m/s |
Masse mobile | 54.9 to 65 kg |
Accuracy of applied energy | ≈ 5% |
Adjustment travel in X | 800 mm (± 400) |
Z adjustment travel | 400 mm (± 200) |
Alpha adjustment travel | 100° (± 50°) |
Test chassis | |
1 test set mounted on 4 castor wheels | |
Base radius | 2,5 m |
Weight of test chassis | 600 kg |
Option: energy verification pendulum | |
Tools | |
4 spherical impactors (Ø25.4, Ø50, Ø70, Ø100) | |
1 impactor extension | |
1 two-component force transducer | |
2 strap shorteners | |
1 pair of 18.5 m straps | |
1 pair of 6.5 m straps | |
Dimensions | |
Length (≠ depending on beam spacing) | 2800 to 3300 mm |
Depth (depending on impactor and skid orientation) | 2 000 mm |
Height | 3 025 mm |
Total weight with electric jack | ≈ 2 200 kg |
Power supply: 400 VAC three-phase + neutral + earth | 16 A |
Customer applications
Would you like to find out more about mechanical test benches? Find out everything you need to know and much more!
COMPLEMENTARY SOLUTIONS
Explore our complementary products to get the most out of your creep test bench! Discover innovative solutions to further enrich your experience and optimize your results.